When you begin a plastics design and engineering project, the goal is to create and manufacture a quality injection molded component. To accomplish that, you’ll want to consider front-ending some essential parts of the designing and engineering process so the actual plastic injection molding manufacturing process will operate smoothly. This will ultimately save you time and money in the long run.
- Select The Right Material
This may be the most straightforward rule of the previous four. Determine what material is right for your part. Is this a medical part? An automotive part? What are the requirements? Does it need to be flexible or rigid? Does the part need to withstand extreme cold or hot temperature? What material do other similar parts use? These questions are just the beginning. Thoroughly research which material works the best for the specific part you’re looking to produce.
- Make Sure The Wall Thickness Is Uniform
Making sure that the wall thickness of your part are as uniform as possible to avoid warpage, sink marks, voids, flow restrictions and longer, uneven cooling times. If uneven wall thickness is essential to the part, try to strive for smooth transitions that gradually taper.
- Try To Avoid Undercuts
Undercuts make it difficult to de-mold your part. The undercut piece of plastic will get lodged inside the mold once the part has hardened and cooled, making it difficult to eject the part from the mold. When undercuts are necessary to the part, and not a byproduct, many manufacturers have lifting mechanisms and side actions to help de-mold the part.
- Try To Avoid Sharp Corners
Try to avoid designing and engineering a part with sharp, squared edges. Sharp edges, like 90-degree angles, produce parts with molded-in stresses. The results are weak points within the part, which leads to cracking and/or part failure. If your part must have a sharp corner, adding a radius or several radiuses will reduce the higher levels of molded-in stress. The radius will redistribute the stress and allow the material to flow more evenly, thus avoiding breakage or failure.
- Make Sure To Consider Warpage And Shrinkage
Materials cool and shrink differently when your injection molded part cools. Warpage and shrinkage are both kinds of distortion that can happen during the cooling process. Warpage distorts the dimensions and is often caused by excess stress on the part itself. Shrinkage occurs when there’s a difference between the linear dimension of the molded part and the mold itself. In order to prevent one or the other, pay close attention to the tooling, part geometry and processing of the part.
About JasonMould Industrial Company Limited:
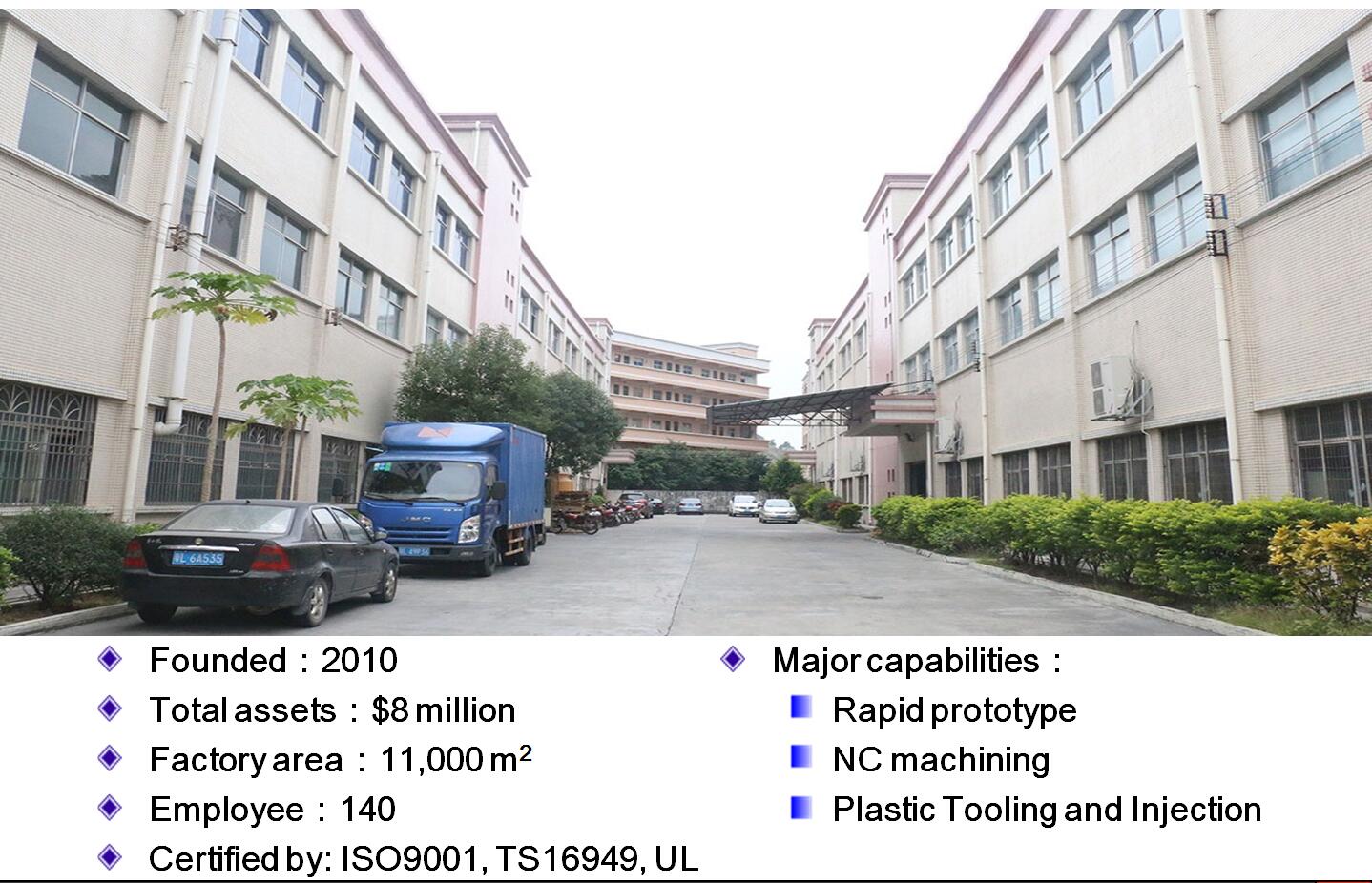
JasonMould is one of the best plastic injection molding manufacturer that offer great services to their clients when it comes to manufacturing advanced molding tools. They export their tools to different parts of the world and have become one of the most famous names in the industrial sector.
Inquiry Contact:
Contact person: James Yuan
Company name: JasonMould Industrial Company Limited
Address: LongGang Village,LongXi Town,BoLuo County,HuiZhou City,GuangDong Province, China
Telephone: 86-752-6682869
Email: info@jasonmolding.com
Website: https://www.jasonmolding.com
Article Original From:https://www.jasonmolding.com/5-ways-to-perfect-your-plastics-design-and-engineering/
没有评论:
发表评论