Double color mold: two kinds of plastic materials are molded on the same injection molding machine, and are molded in two times, but the products only die once. Generally, this molding process is also called double injection molding, usually by a set of molds, and a special two-color injection molding machine is needed.
Overmold: two kinds of plastic materials do not have to be injected into the same injection machine and are molded in two times. After taking out the mold from a set of moulds, the product is then placed in another set of moulds for second injection molding. Therefore, the general molding process is usually done by two sets of molds instead of a special two-color injection molding machine.

Double color mold and overmold overview: the design should pay attention to the positioning of overmold, need to make the adhesive sealing and the reverse slope on the rubber parts to prevent the deformation of the glue. Double color mold is becoming more and more popular in the market at present. This process can make the appearance of the product more beautiful, easy to change color but can not be sprayed, but the cost is expensive, also needs high technical requirements.
- The two shapes of Cavity are different, forming one kind of products respectively. And the two shapes of the Core are exactly the same.
- the front and rear mould of the die must be 180degree after the center rotates. This check action must be done at design time.
- pay attention to the position of the pinhole of the top, the minimum distance 210mm. Large mold must be properly increased the number of rod holes. Moreover, because the thimble attached to the injection molding machine is not long enough, we must design an elongated thimble in the mold, and the thimble will grow about 150mm of the mold base. 2 positioning rings must be designed on the back die floor.
- the total thickness of the front panel plus A board should not be less than 170mm. Please take a closer look at other reference data of this type of injection molding machine, for example, the maximum thickness of the injection mold, the minimum thickness of the mold, the distance between the top hole and so on.
- the water outlet of the three plate die is preferably designed to be automatically demoulding. Special attention should be paid to whether the ejection action of the soft rubber nozzle can be *. 6. the depth of the SPRUE in the front side does not exceed 65mm. The distance from the top of the upper side (SPRUE) to the center of the mold is not less than 150mm.
- in designing second injection moulded CAVITY, we can design a part of avoiding the first place of the product that has been molded by CAVITY. However, it is necessary to carefully consider the strength of each sealing site, that is, in the injection molding, will there be a plastic deformation under the large injection pressure, which may lead to the possibility of a batch front in the second injection molding.
- in designing second injection moulded CAVITY, we can design a part of avoiding the first place of the product that has been molded by CAVITY. However, it is necessary to carefully consider the strength of each sealing site, that is, in the injection molding, will there be a plastic deformation under the large injection pressure, which may lead to the possibility of a batch front in the second injection molding.
- injection molding, the first injection molding product size can be slightly larger in order to make it in the second molding can be more tight with the other CAVITY, in order to meet the sealing effect.
- pay attention to whether the flow of plastic will be impulsive in the second injection process, so that the first molded product will deform its glue position. If this is possible, we must try to improve it.
- before A or B plate clamping, pay attention to whether the front mold Slider or Lifter will first reset and crush the product. In this way, we must try to make the A and B boards die first, then the SLIDER or LIFET of the front die can be reset.
- two CAVITY and CORE water distribution as far as possible, and balanced, the same.
12.99% situarion is to first inject the hard rubber part of the product, and then injection the soft rubber part of the product. Because the soft glue is easy to deform.
About JasonMould Industrial Company Limited:
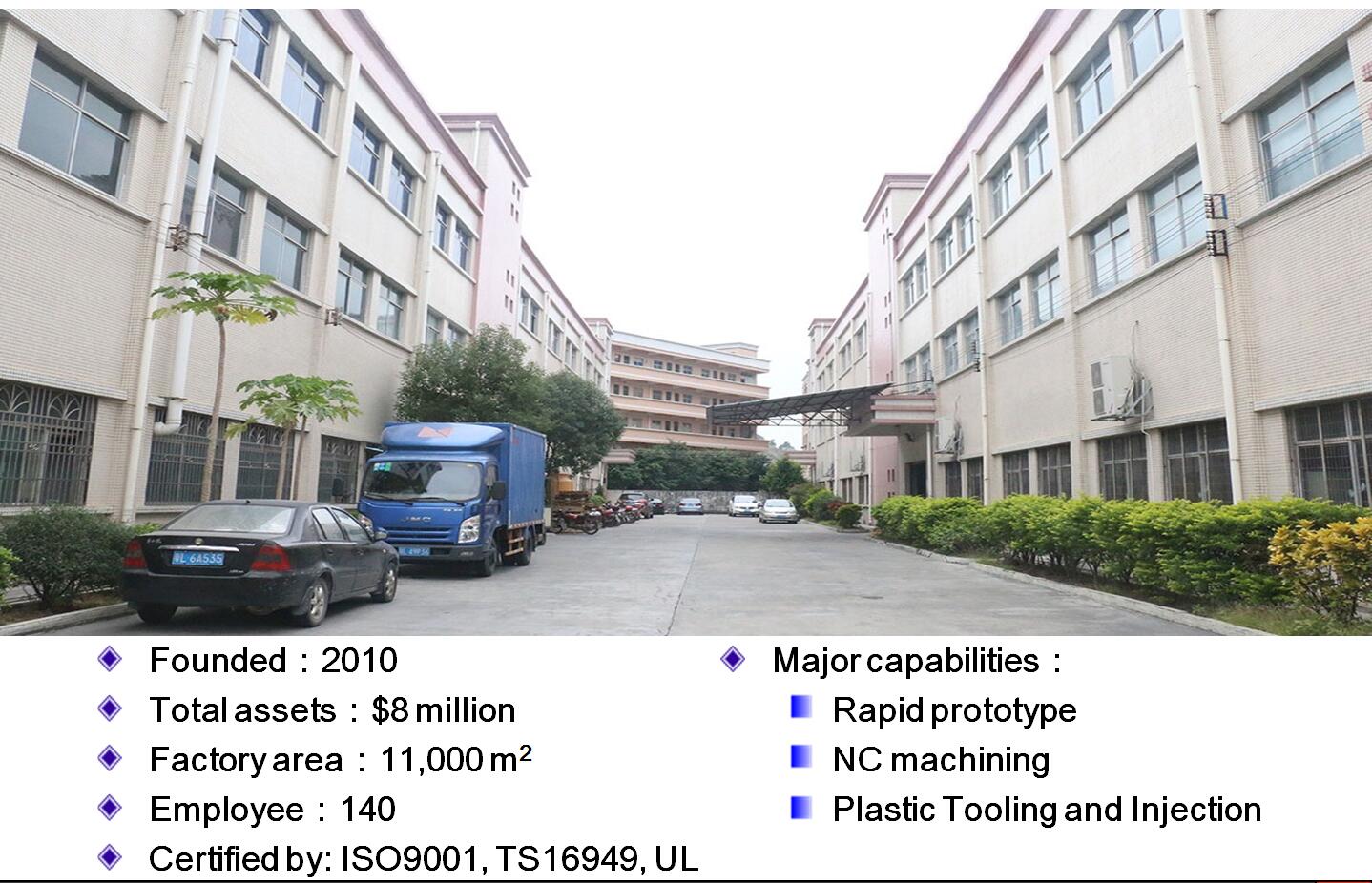
JasonMould Industrial Company Limited is a leading plastic injection molding manufacturer in China. The company had established in the year 2010. The company has made a reputation of being one of the finest plastic mold producers in China. They are great at making medical equipment, appliances, electronic equipment and even safety equipment.
For more about custom manufacturer of plastic molding products,please visit https://www.jasonmolding.com/
Inquiry Contact:
Contact person: James Yuan
Company name: JasonMould Industrial Company Limited
Address: LongGang Village,LongXi Town,BoLuo County,HuiZhou City,GuangDong Province, China
Telephone: 86-752-6682869
Email: info@jasonmolding.com
Article Original From:https://www.jasonmolding.com/differences-between-double-color-mold-and-overmold/