Helpful Information for Injection Molding
Injection mold manufacturing plays a key role in a wide range of production engagements. One of the biggest benefits of this type of process is seamless mass production. Implementing injection mold manufacturing in your output cycle enables your business to replicate an infinite number of the same component in succession and with flawless results.
Beyond granting the ability to mass-produce specific parts/components, injection mold manufacturing also delivers many other benefits. An advantage to using this production option in a wide range of industries is the low amount of waste. Unlike traditional tactics that leave significant portions of materials behind after the cycle is complete, injection molding minimizes scrap remains. As a result, many business owners find this procedure both efficient and budget-friendly.
What To Consider Before Moving Forward With This Approach
While this type of manufacturing method delivers a wide range advantages, there are a few critical factors to consider before determining if it’s the right approach for your project. Some considerations include:
Initial Tooling
The initial tooling means designing and prototyping a mold tool. This requires working with a trusted partner to create the tooling to make a precise final piece to use for replication.
Lead Times
Once the prototype design is complete, output occurs rapidly. However, ramping up and working through tooling does take time. When considering various manufacturing options, you will have to evaluate lead times to know if you have the bandwidth for this type of process.
Changes in Design
Additionally, you will also want to consider if your design might change throughout the process. Once you’ve created the prototype, you will not be able to modify it without beginning the tooling process all over again. Changing your initial design may result in waste and scrap or even require you to start over completely, resulting in loss of both time and money.
Size of Product
The size of the product you wish to mass-produce can also have an impact on the manufacturing method you will use. Injection mold manufacturing works best with smaller items that can be created in a single cycle. If you require tooling for larger items that may need multiple cycles, you may want to think about other output options.
Choose the Right Provider
Perhaps the biggest consideration when selecting the right production method for your engagement is choosing the right manufacturer for your job. When screening through prospective vendors, look for a company that has extensive experience in your specific vertical. Knowing that your entrusting your business to a team with previous industry insight can have a major impact on your overall engagement. Some vendors may seem less expensive at first; however, moving forward based solely on price with a firm that doesn’t have the experience needed for efficiency can actually cost more in the long run.
About JasonMould Industrial Company Limited:
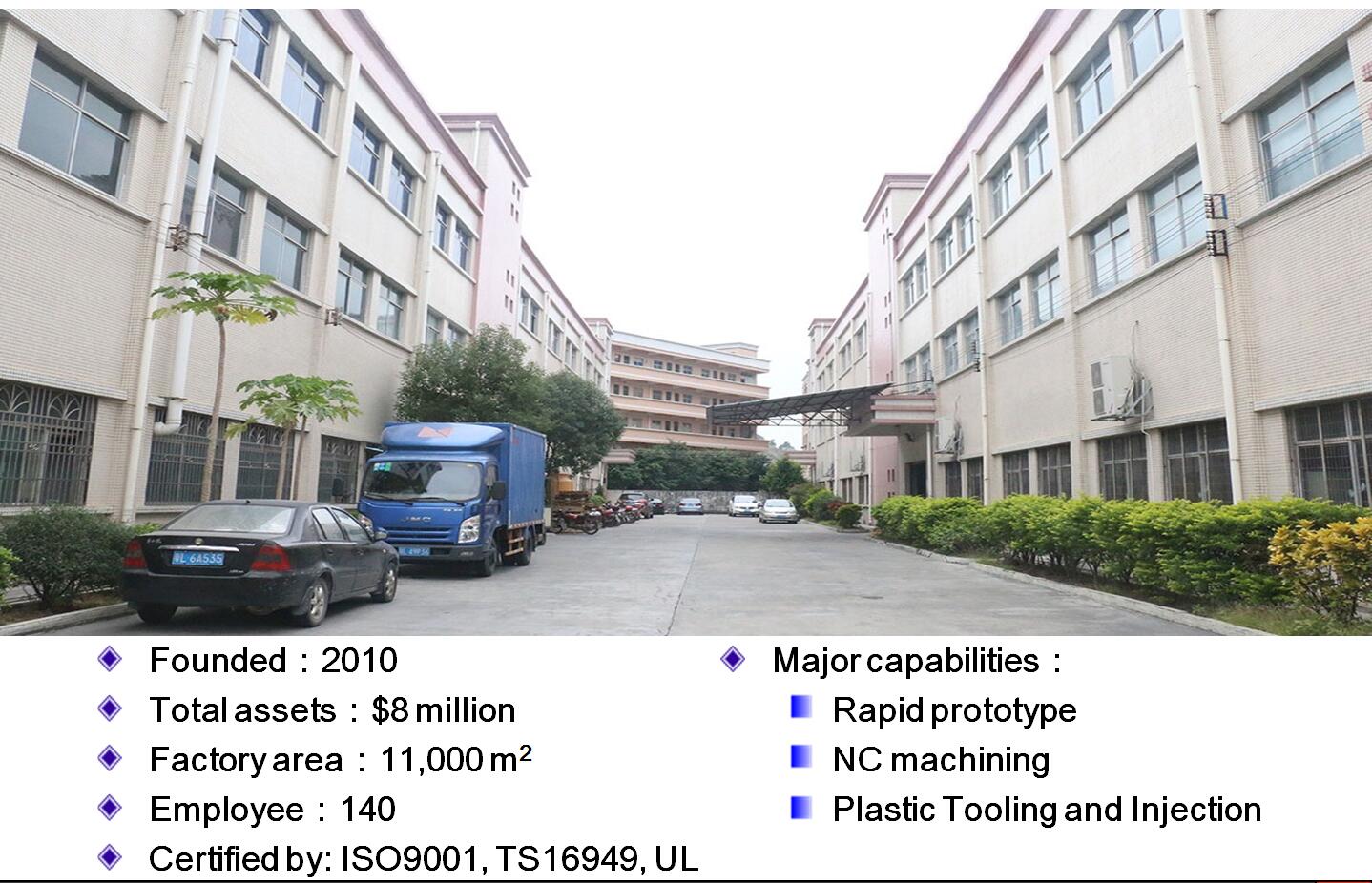
JasonMould is one of the best plastic injection molding manufacturer that offer great services to their clients when it comes to manufacturing advanced molding tools. They export their tools to different parts of the world and have become one of the most famous names in the industrial sector.
Inquiry Contact:
Contact person: James Yuan
Company name: JasonMould Industrial Company Limited
Address: LongGang Village,LongXi Town,BoLuo County,HuiZhou City,GuangDong Province, China
Telephone: 86-752-6682869
Email: info@jasonmolding.com
Website: https://www.jasonmolding.com
Article Original From:https://www.jasonmolding.com/injection-mold-manufacturing-what-you-need-to-know/